The Energy Efficiency Inspection Process: What Builders Should Expect
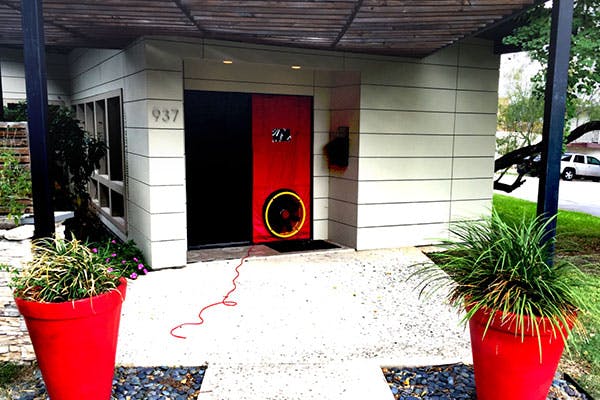
The homes you build today need to do more than just look good and stand strong; they also need to adhere to certain energy efficiency standards. With the intensifying focus on environmental sustainability and cost-saving measures, keen attention must be paid to how energy-efficient a building is. This crucial task is where an energy efficiency inspector, such as Force Energy Solutions, comes into play.
FES conducts detailed checks on newly constructed or renovated buildings to ascertain their level of energy efficiency. We perform comprehensive tests such as envelope pressure tests, duct tests and insulation inspections. But what should you as a builder expect from these important inspections? Let's take a look.STEP 1: Plan Review
Your FES inspector will carry out a meticulous examination of your building project to identify how effectively it conserves energy. Evaluating the efficiency of your heating, cooling, ventilation systems, and insulation, we'll also measure how the structure’s envelope – the physical separator between the interior and exterior environment of your building – contributes towards energy conservation.
We'll need your plans, construction specs, and a manual j to get started, and FES will provide a Projected Energy Compliance Report upon completion of this step.
STEP 2: Insulation Inspection
After insulation is installed, and before drywalling starts, we'll perform a thorough analysis of the quality and condition of the insulation within your building. We scrutinize wall cavities, roof systems, top plates, and floors to evaluate the effectiveness of thermal control within the building.
From this examination, the builder should grasp whether the insulation used is of suitable quality, appropriately installed, and adequate for the building's size and geographical location.
STEP 3: Duct Testing
At the same time as the insulation inspection, we will test the hvac system to determine if there is any air being lost through the ductwork. All supply grills need to be installed for this test, and we will need power to run the duct blaster, which will pressurize the duct system to measure the air leakage rate.
We will point out any inefficient designs, impaired ducts or areas that need repairs. This information can serve as a roadmap for improving the efficiency and longevity of the HVAC system, and prevent issues for your home buyer down the road.STEP 4: Envelope Pressure Testing
Prior to calling in the cleaning crew, the builder should schedule a Final inspection with FES, where we'll perform an envelope pressure test, also known as a Blower Door Test. This is how we measure the amount of air escaping from or entering into the building –– using a powerful fan mounted to a screen on a building's exterior door, FES will depressurize the house, causing the outside air to flow through any unsealed cracks and openings, revealing air leakage sites.
The builder should expect FES to assess the quality of the building's sealing against undesired air intrusion or leakage. Builders should pay close attention to these findings as they often have a significant impact on the building’s overall comfort, energy efficiency, and resilience.
STEP 5: Final Reporting
After the site visit, your FES inspector will provide a detailed report of their findings, along with any forms you need to upload to the city, and a Confirmed Energy Compliance Report.
As a builder, you should expect this report to help you further understand the building's energy performance and guide you in making improvements to enhance energy efficiency.
Energy efficiency inspections are crucial elements of modern-day building projects. They ensure that buildings comply with environmental sustainability norms and help reduce energy consumption in the long run. As a builder, understanding these inspection processes and what to expect from an efficiency inspector can pave the way for constructing energy-efficient, sustainable, and comfortable buildings.